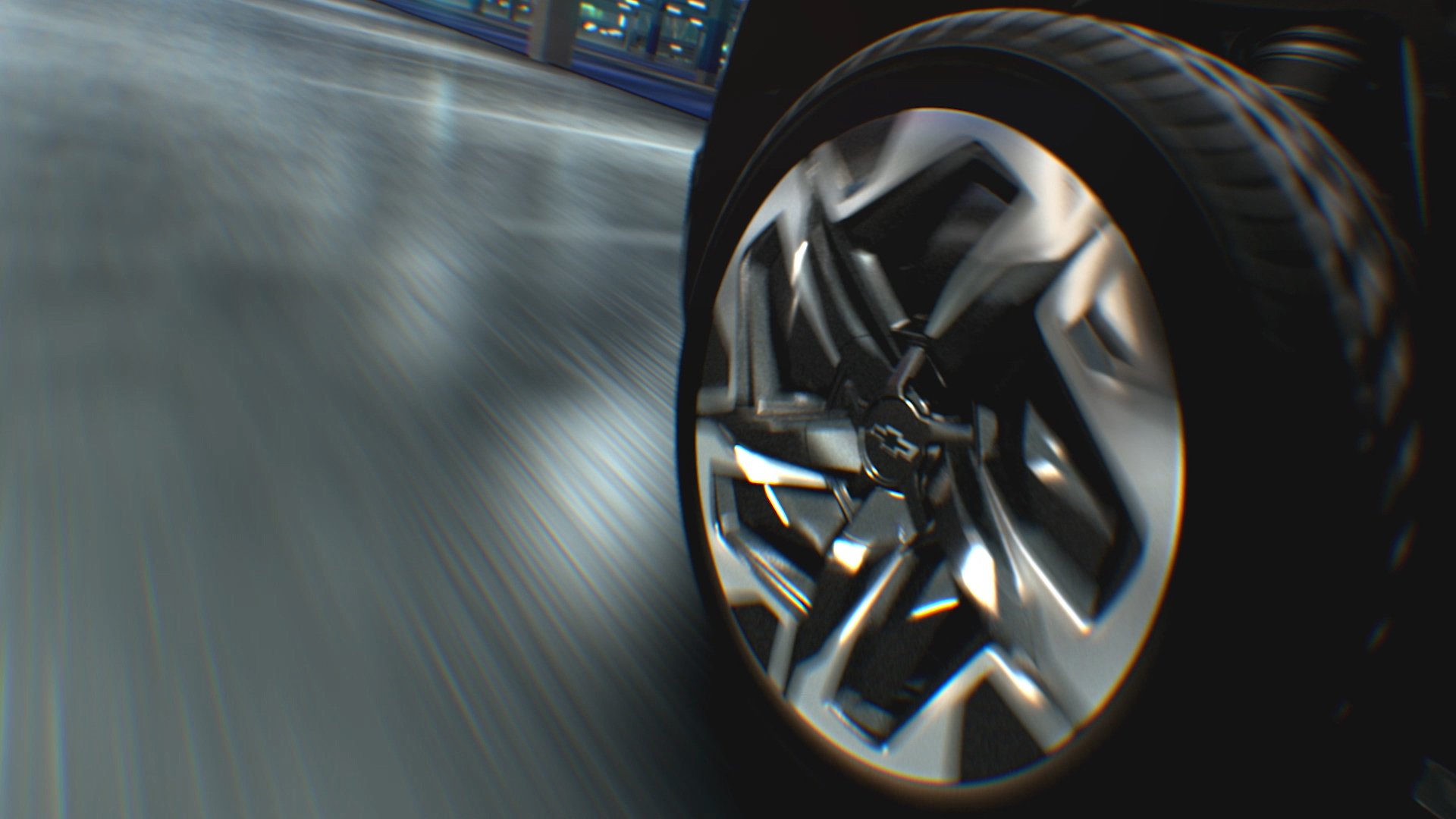
article discussing the implications of stripped or corroded bolts and the importance of selecting high-quality fasteners in the automotive and construction industries.
Stripped or Corroded Bolts: The Bane of the Automotive and Construction Industries
Fasteners, such as bolts and nuts, are critical components of both the automotive and construction industries. These tiny components hold together larger, heavier parts of machinery and equipment, providing the necessary stability, strength, and safety.
However, fasteners are not immune to wear and tear, corrosion, and damage. One of the most common problems encountered by mechanics and technicians is stripped or corroded bolts, which can cause significant delays, increased costs, and safety hazards.
One recent example is the case of a GM-Trucks.com user who attempted to replace the steering wheel in their custom Silverado with a high country steering wheel. Unfortunately, during the process, they ended up rounding out the torx bolt, rendering it useless. The local mechanic they consulted advised them that the bolt was too hard to drill.
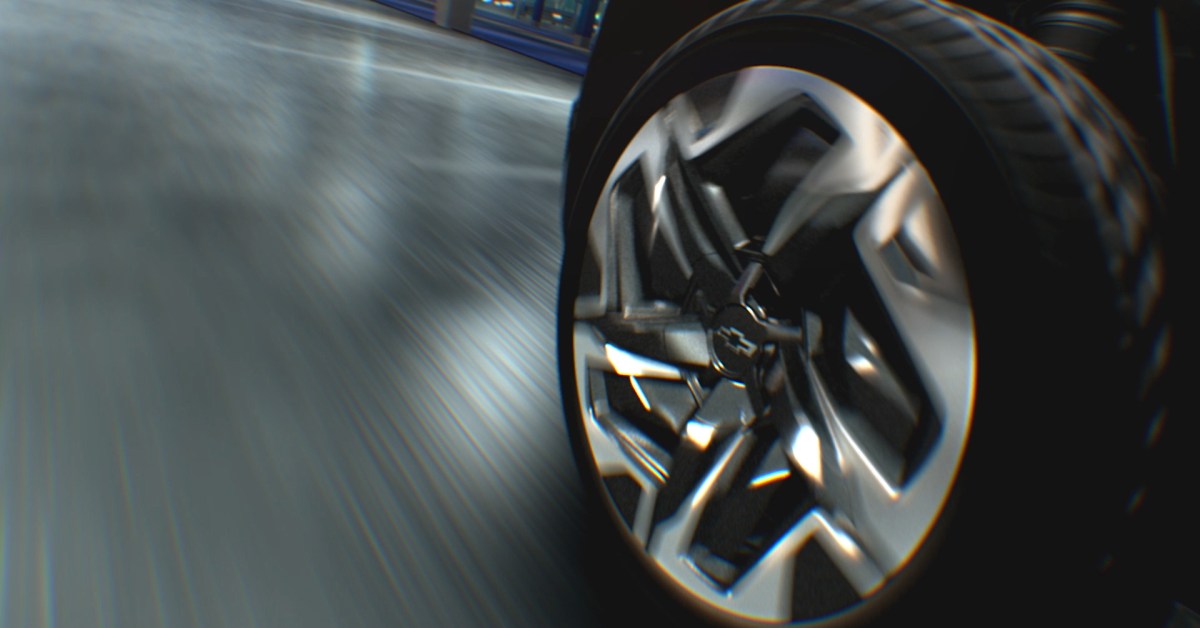
While this may seem like a minor inconvenience, stripped or corroded bolts can have significant implications, especially in high-stress applications such as automotive and construction machinery. For instance, if bolts in critical areas of an engine or transmission fail, it can lead to catastrophic failures such as engine seizure or transmission failure.
Similarly, if bolts holding together building structures or heavy equipment corrode or become loose, it can lead to structural damage, collapse, or machinery malfunction, potentially causing injury or death.
Therefore, the quality, integrity, and durability of fasteners are paramount in ensuring the safety and reliability of machinery and equipment. Considering the high stress, vibration, and environmental conditions that fasteners are exposed to in the automotive and construction industries, selecting subpar or low-quality fasteners can result in severe consequences.
The Importance of Selecting High-quality Fasteners
To prevent stripped or corroded bolts and ensure the longevity and safety of machinery and equipment, it is crucial to select high-quality fasteners. Here are some factors to consider when choosing fasteners:
1. Material: The material of the fastener should match the strength and environmental conditions of the application. For instance, stainless steel or high-grade alloy steel fasteners are ideal for applications that require resistance to corrosion and heat.
2. Coating: Fasteners can be coated with different materials such as zinc, cadmium, or chrome to improve their corrosion resistance. Selecting the appropriate coating depends on the application and the environment in which it operates.
3. Strength: Fasteners come in different strengths, measured in psi or pounds per square inch. Choosing fasteners of the appropriate strength is essential to prevent failure or stripping.
4. Size: Fasteners are available in different sizes, thread types, and pitch, and choosing the right size and type of fastener is critical to ensure a proper fit and prevent overloading or stripping.
5. Quality: Buying fasteners from a reputable, certified manufacturer can ensure the quality, reliability, and consistency of the product. High-quality fasteners undergo rigorous testing and certification to meet or exceed industry standards, ensuring their integrity and durability.
For instance, the Fortune Group, a company specializing in the production of bolt and nut, king pin kits, and undercarriage parts for construction machinery, supplies high-quality fasteners to OEM machine brands such as Mercedes Benz, Weichai, Sino Truck, KOBELCO, SHANTUI, among others. With 36 years of experience in the industry, Fortune Group has established a reputation for producing reliable, high-quality, and durable fasteners that meet or exceed industry standards.
In conclusion, stripped or corroded bolts are a common but preventable problem faced by technicians, mechanics, and engineers in the automotive and construction industries. Choosing high-quality, appropriately sized, and strength-rated fasteners, especially from reputable manufacturers such as the Fortune Group, can prevent downtime, costly repairs, and potential safety hazards, ensuring the reliability and longevity of machinery and equipment.